Steel & the circular economy: the challenges of carbon-free automotive steel production
Context
The necessary electrification of the car fleet requires a reduction in the carbon footprint of electric vehicles, whose second largest greenhouse gas (GHG) emission, after the battery, is steel, which makes up an average of 70% of the vehicle. The automotive industry consumes 25% of the steel produced worldwide, while global steel production is responsible for 8% of GHG emissions.
While most steel is currently produced by traditional means using blast furnaces, which consume a lot of coal and emit a lot of CO2, new technologies such as the direct reduction of iron ore with hydrogen (H2-DRI) in electric arc furnaces (EAF) are making their appearance, and are being widely integrated into steelmakers’ decarbonisation strategies.
EAFs allow increased use of steel scrap, which could complement H2-DRI to help reduce the carbon footprint of steel production, while limiting the extraction of primary raw materials.
This interest in increasing the use of recycled steel is particularly well represented by certain car manufacturers in order to reduce emissions from their supply chain and reduce their dependence on certain supply chains.
These initiatives are encouraged by the European regulatory framework, in particular by the revision of the end-of-life vehicles Directive, which aims to strengthen circularity requirements from design to management of ELVs. The Commission’s current proposal mentions setting mandatory recycled content targets for steel, the proportion of which has yet to be defined.
The challenge of incorporating more scrap into steel production today lies in quality, which must be sufficient to meet technical standards. Today, scrap from ELVs is too polluted with materials such as copper or aluminium to produce the flat steel used in car manufacturing.
Description
The aim of the project is to assess the potential of the ELV sector to supply high-quality scrap compatible with EAF (with or without DRI) in order to promote the decarbonisation of steel production for the automotive industry.
The aim is to contribute to the Commission’s discussions on the introduction of a minimum threshold of recycled steel in new vehicles.
In collaboration with Indra, a major player in recycling in France, the ITM carried out in-depth dismantling of 300 ELVs representative of the current French fleet in order to identify the technical conditions (additional dismantling, advanced post-shredding, best eco-design practices, etc) for obtaining high-quality scrap metal. Protocols have been added to the usual dismantling processes to extract as many pollutants as possible from the steel, particularly copper and aluminium. The additional costs generated by this process and the added value derived from the extracted materials were also assessed.
These deep-dismantled ELVs have been shredded and are currently being analysed in an independent laboratory (IRT Metz) to assess the quality of the scrap and its suitability for use by the automotive industry in the production of new vehicles. A sample has also been sent to a steel manufacturer for testing under actual steel coil production conditions.
This project will make it possible to assess (1) whether the additional labour costs involved in deep-dismantling are offset by higher revenues from the secondary materials generated, (2) the quality and quantities of copper and aluminium that can be recovered, and (3) the quality of the scrap obtained and its compatibility with EAF.
The trial could thus justify the generalisation of these new practices, as well as the need to improve eco-design.
The ITM interacts with various players in the value chain on these subjects, in particular with industrial players, in order to gather different perspectives and understand the many strategic issues at stake. We also maintain a global vision of the decarbonisation of steel production thanks to our close links with IDDRI and deep-decarbonisation pathways (DDP).
Team
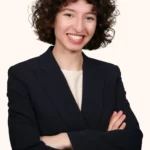
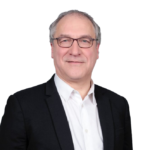